Conservation Journal
Spring 2007 Issue 55
Surreal semi-synthetics
The V&A's major spring exhibition Surreal Things: Surrealism and Design is the first to explore the influence of Surrealism on all aspects of design including theatre, interiors, fashion, film, architecture and advertising. Surreal Things features nearly 300 objects - furniture, paintings, sculpture, architecture, jewellery, ceramics, photography, graphics, film, fashion and textiles drawn from the V&A's collections and from public and private collections around the world. The exhibition focuses on the work of Surrealist artists and designers active before 1939 and follows their careers after the war.

Figure 1. S.860-1980 ‘The General’ from Le Bal designed by Giorgio de Chirico, 1929 © DACS, London 2006 (click image for larger version)
The world of theatre and fashion is well represented: the exhibition begins with a selection of costumeand set designs for Ballet Russes productions in the 1920s and early 1930s by the artists Giorgio de Chirico, Joan Miró and André Masson and ends with a stunning 'catwalk' of couture costumes (Figure 1). The witty fashion designs of Elsa Schiaparelli are featured, including the famous 'Tear' dress on which she collaborated with Salvador Dali (Front cover image). Also on display are a number of costumes by Charles James including his influential 'pneumatic' satin evening jacket.
Prior to the exhibition, all the V&A's costume and textile exhibits arrived in the Textile Conservation Studio for treatment and mounting. They included seven ballet costumes, eleven couture costumes, six accessories and nine printed textiles. Several costumes required extensive conservation treatment and all of the costumes required mounting on mannequins for display. Two fibre-glass mannequins were specially commissioned to mimic the poses of ballet dancers as captured by contemporary photographers. The mannequin for the character of Fate from the 1932 ballet Les Presages leaps in the air and the mannequin for the Spinning Top from Jeux d'enfants actually spins on 'pointe' rotated from below by a motor (Front cover image). The knitted wool leotard worn by Fate has pale bulging 'eyes' stitched to the hood, which have a distinct resemblance to ping-pong balls cut in two. Brenda Keneghan, Senior Polymer Scientist, analysed the material using Fourier Transform Infrared Spectroscopy (FTIR). The results revealed that the eyes are made from cellulose nitrate, the first semi-synthetic plastic material. Many more semi-synthetics were to be found amongst the Surreal Things costumes, although they were not all as immediately obvious as Fate's eyes.
Alexander Parkes is credited with the invention of the first cellulose nitrate based plastic, which he called Parkesine. At the 1862 Great International Exhibition he exhibited a variety of Parkesine objects as diverse as combs, billiard balls, buttons, imitation tortoiseshell and false teeth. The material was made by treating cellulose with nitric and sulphuric acids to produce cellulose nitrate; plasticisers were then added so that the material could be moulded. In the following years, Hyatt in the USA developed Celluloid from cellulose nitrate plasticised with camphor and by the 1880s Celluloid was being used by the clothing industry to make detachable, easy to clean collars and cuffs.
Cellulose nitrate was also used to produce the first artificial fibres; it was dissolved in alcohol and ether to produce a solution of collodion, which was then squirted through a series of fine holes (in a 'spinneret') to produce long filaments that solidified in warm air. The filaments were then treated with ammonium hydrogen sulfide to convert them back to cellulose. During the 1890s Count de Chardonnet became the first successful manufacturer of this new fibre and named it Chardonnet silk. Once this process for creating artificial fibres was established, new methods were discovered for dissolving cellulose that did not involve nitration. The 'cuprammonium' process, by which cellulose was solubilised using copper sulfate, ammonia and caustic soda, was developed in 1890 but did not achieve commercial success until 1919 when a very fine yarn was developed making it possible for the fibre to compete with the viscose process, which was more economical. The viscose process was patented by Cross and Bevan in 1892. In this process cellulose was degraded with caustic soda then treated with carbon disulfide resulting in a viscose solution. The fibres were converted back to cellulose in a chemical bath. Cotton linters or purified pulp from trees is the most common source of the cellulose used in the production of regenerated cellulose fibres. These new methods replaced the Chardonnet process, slow and dangerous due to the explosive nature of cellulose nitrate.
Until the 1920s man-made fibres were commonly referred to as 'artificial silks'. The name 'rayon' was derived following a nationwide competition in the USA in 1925. It was initially used to describe all man-made fibres but is now used when referring to cuprammonium rayon and viscose rayon. These fibres are similar to each other because they are both converted back into cellulose. The other fibre developed during this period, cellulose acetate, often sold under the brand name 'Celanese', differs from the regenerated celluloses because it is not converted back into cellulose after processing. It is classified as a derivative of cellulose with a different chemical structure and properties.
Cross and Bevan also worked on the development of cellulose acetate in 1894. They developed a version known as triacetate, as three of the hydroxyl groups in each unit of the cellulose molecule have been substituted with acetate groups. Cellulose triacetate proved to be difficult and expensive to produce as it was only soluble in a few chemicals and these were toxic. It was not until the 1950s, when a more suitable solvent was found for triacetate, that the latter became commercially important. In 1906 scientists discovered that triacetate could be modified into a substance which could be dissolved in acetone, a readily available and less toxic solvent. This modified fibre is sometimes referred to as diacetate but it actually has an average of two and a half acetate groups per unit. During the years preceding the First World War cellulose acetate was developed as a fibre and also as a lacquer. In 1916 the British government sponsored two Swiss brothers, Henri and Camille Dreyfus, to open a factory producing cellulose acetate lacquer to coat the fabric wings of aircraft. At the end of the war they turned their attention to producing fibres and were manufacturing Celanese by 1921. Cellulose acetate was also developed for use in a 'plastic' form like celluloid but was not in production until the late 1920s.
Figure 3. T.36-1964 ‘Etruscan’ dress by Elsa Schiaparelli, 1935/6, cellulose nitrate zip Photography by Elizabeth-Anne Haldane (click image for larger version)
The majority of the couture costumes in the exhibition date from the 1930s. By this time the production of these cellulose-based textile fibres was well established and the quality had improved as technology advanced. The regenerated cellulose fibres have similar properties to cotton but chemical modification during processing produces a change in the physical characteristics of the fibres. They are not as strong as cotton and have relatively poor wet strength but they all have excellent draping qualities, are soft to the touch and are shiny like silk. Manufacturing methods were also developed to produce a duller, less shiny fibre so that the product would have a wider range of end uses. The filament could be cut into small pieces and spun together to produce a 'staple' yarn, other methods included incorporating de-lustering agents into the fibre or applying 'finishes' to the fabric. The rayon fibres can be dyed with the same dyes that are used for cotton because they are all made from cellulose, but new dyes had to be developed to dye cellulose acetate fibres because of the difference in their chemical structure.
Elsa Schiaparelli and Charles James both worked with textile manufacturers to develop new fabrics for their couture garments and often endorsed products as well. Schiaparelli is said to have popularised the use of rayon, particularly through the use of interesting weaves that added texture to the fabric. She is also well known for her enthusiastic use of plastics to make jewellery, and as buttons and trimmings on her garments.

Figure 4. T.394-1974 ‘Skeleton’ dress by Elsa Schiaparelli, 1938, cellulose acetate ‘Éclair’ zip Photography by Elizabeth-Anne Haldane (click image for larger version)
It is interesting to see how many blended silk and rayon fabrics were found amongst the costumes including the 'Tear' dress (Front cover image). In a blend, fibres are mixed together during the spinning process to produce a new yarn that benefits from the properties of both fibres. This is different from the fabric in the 'Column' dress where the weft is one fibre, cuprammonium rayon and the warp is silk. The Charles James jacket is made from cellulose acetate. This fabric, referred to as 'slipper satin', is smooth with a soft sheen that emphasises the three-dimensional qualities of the jacket. An interesting form of rayon, supporting the satin columns in the 'Column' dress, was found by Alice Cole, RCA/V&A Conservation student, during treatment (Figure 2). The columns are lined with a loose mesh fabric, the imprint of which can just be seen on the dress fabric. This mesh was probably made to imitate and improve upon horsehair, which was often incorporated into fabrics to stiffen them. The rayon fibre in the mesh looks like nylon fishing line but pre-dates nylon, the first truly synthetic fibre, which was launched onto the market in October 1938.

Figure 5. T.393-1974 ‘Tear’ dress by Elsa Schiaparelli, 1938, cellulose acetate ‘Éclair’ zip Photography by Elizabeth-Anne Haldane (click image for larger version)
Acknowledgements
With thanks to my colleagues in the Textile Conservation Studio who have worked on Surreal Things: Surrealism and design and to Brenda Keneghan and Emma Richardson, Science Section, and V&A curators, Ghislaine Wood, Alexander Klar, Sonnet Stanfill and Jenny Lister, and to Dilys Blum, Philadelphia Museum of Art.
References
1. Richardson, E. 'Towards on-site collections management: NIR characterisation and condition monitoring of textiles', V&A Conservation Journal , no 54 (Autumn 2006), p. 12
2. Handley, Susannah. Nylon, The Manmade Fashion Revolution , Bloomsbury Publishing Plc (1999), p.27
Blum, Dilys, E., Schocking! The Art and Fashion of Elsa Schiaparelli , Philadelphia Museum of Art, (2003)
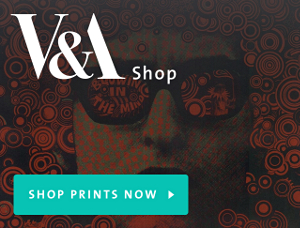
Spring 2007 Issue 55
- Editorial Comment - Conservation Journal 55
- Stein Mellon Textile Project at the V&A
- Storage of the Stein Loan Collection
- Discoveries on a pair of cassoni
- Treatment of two Coptic tapestry fragments
- Surreal semi-synthetics
- Investigation of the patina on Bidri using advanced surface analysis techniques
- Printer friendly version