London Design Festival at the V&A 2013
Audio: What is the Future of 3D Printing

‘Liberator’, 3D printed gun. Cody Wilson / Defence Distributed, 2013
As part of the London Design Festival at the V&A, the Science Museum joined forces with the V&A to present an inspiring panel discussion on the future of 3D printing. A panel of scientists and technical experts discuss their views on 3D printing, addressing questions such as what is most exciting in 3D printing at the moment, and what may be possible in the future.
The event was chaired by Pippa Hough, Content Developer at the Science Museum. The panel featured a variety of 3D printing experts, from a broad range of fields:
Dr Adrian Bowyer, a former senior lecturer in the Mechanical Engineering Department at the University of Bath, and Inventor of the RepRap open source printer ("self-replicating rapid prototyper").
Dr Phil Reeves, Managing Director of print consultants Econolyst, a 3D printing consultancy and research firm that advises on future business, technology strategy and the benefits of AM (Additive Manufacturing) adoption.
Prof Richard Hague, Professor of Innovative Manufacturing, and Director of EPSRC Centre for Additive Manufacturing, Faculty of Engineering, Nottingham University.
Prof Mark Miadownik, materials scientist, engineer, broadcaster and writer at University College London.
PH: Good afternoon everybody and welcome to ‘What is the Future of 3D Printing?’ My name is Pippa Hough and I am an Exhibitions Developer at the Science Museum and I work on our News Gallery. We are currently in the final stages of putting together an exhibition all about 3D printing called ‘3D: Printing the Future’. The exhibition is going to contain over 700 items, from prosthetic limbs to jewellery, which I am sporting today. We’ve got some other bits and pieces as well: we’ve got some architectural models, we’ve even got 3D printed drugs - yes, that is a thing! We are also including the rather controversial 3D printed gun that some of you may have heard of - it has been mentioned a little bit in the media. We’ve had it on display for the last few months in our News Gallery and we have been engaging visitors with the ever-more-complex question: “should we be able to download anything?” We’ve taken the feedback visitors have given us on that, and we’re incorporating it into our exhibition so you can come and see what everyone thought. We’ve been working with some wonderful people to develop our exhibition and a few of them are here today to have a chat about the future of 3D printing. We’re going to be discussing the fascinating present and the intriguing future of 3D printing.At the end here we have Adrian Bower who is from the RepRap Project; we’ve got Phil Reeves, who is the Managing Director of 3D printing consultancy Econolyst; Richard Hay who is the Director of the EPSRC Centre for Innovative Manufacturing [in Additive Manufacturing] at Nottingham University and finally we have Mark Miadownik who is the Director of UCL’s Institute of Making.Do you want to each say a little bit about why you’re here and why we might have invited you? Do you want to start, Adrian?
AB: Shall I start? Yes. Well, as I’ve been asked to introduce myself, I think I’d better start with a lie: I’m not actually that interested in 3D printing! As I say, that is actually a lie, but I’ll explain it in a moment. I’m fascinated by the whole subject - it seems to me to be a really interesting technology. But the way I came to it was because I’m much more interested in self-replication and making a machine that can copy itself, so in 2004 I started a project called the RepRap Project: RepRap is short for Replicating Rapid Prototyper - Rapid Prototyper is ‘engineer-speak’ for a 3D printer - and that project was an open source project that involved everybody that wanted to volunteer from all over the world, to put together a design for a 3D printer that would print itself. In 2008 we had our first machine working and it made a set of parts for the machine that was to be its descendant. It doesn’t make all of its own parts: not counting nuts and bolts it makes about 48% of its own parts, a respectable percentage. This child machine, we put it together, and it very nearly worked. It didn’t work because we’d made a mistake in cutting a piece of belt that ran round it to drive one of the movements in the machine so we promptly designed a little part to tension up the belt, got the machine to print it itself while we held a screwdriver against the wrongly cut belt, and the very first thing that the descendent machine made was a grandchild part for itself. So we’re on course to having a technology that’s self-replicating and that’s the thing that interests me. That’s my route into 3D printing.
PH: Wonderful. Phil, if you want to explain what this is. [The Christmas tree in the corner]
PR: Right, yes, that’s the Narcissistic Boss Christmas Tree, which if you have access to 3D printers and scanners I would encourage anyone to print one out and annoy your friends and neighbours with it, and then when the Science Museum rings up and says “Can we steal it off you?” you say “By all means, take it away, don’t let me ever see it again!” Anyway, 3D printing, so my route’s been a little bit different I think to Adrian. We’ve been involved in this for about 20 years and Adrian mentioned prototyping, rapid prototyping, which is where all this technology started. You know, this isn’t a new phenomenon: it’s a 29-year-old technology that’s been embedded into industry for decades. We’ve been working, using this technology, really supporting design innovation prototyping; it’s engineering insurance, that’s what this technology is. About ten or 12 years ago there was a bit of an epiphany I think when somebody, a colleague that we know, sort of postulated this idea that you could make products. Why do we just make prototypes? You know, it’s illogical, why don’t we make products? And it was sort of heresy at the time, you know the idea that you could use these machines to make products, ‘cause that’s what injection moulding machines are for, or CNC machines are for, and playing around with the idea we actually realised that it does make a lot of sense and when you look in a lot of depth at this you realise that there’s a lot of social, economic, environmental benefits to transitioning away from traditional manufacturing approaches and using an additive approach to make products. That’s what we do as a company now: we advise no end of businesses around the world on, not just how to make these machines, but how to use and how to apply them into the value chain, into the retail chain, into the supply chain, and how you actually get products coming out that are fit for purpose, for consumers to buy. That’s our background history.
PH: Lovely. Right, Richard.
RH: Hi my name’s Richard Hague, I’m at the University of Nottingham and I started this also 20 years ago. Actually Phil and I did our PhDs together, taking slightly different paths from this way forward…
PR: The office next door.
RH: The office next door! My interest in the area came from… I used to work in the oil and gas industry as a graduate and then I came across this stereolithography process at a conference, and I thought that’s got to be more interesting than the job I’m doing now, so I gave that up to do a PhD at Nottingham. I went through the whole rapid prototyping gaze and I guess our group was of the first to look at this Rapid Manufacturing, as it was called then, and I’ve had really an interest in the Additive Manufacturing side of things so for me there’s a difference between the low-end 3D printing and the higher end Additive Manufacturing - which I think we’re probably going to get to. We as a group have a focus on Additive Manufacturing. There’s lots you can do with it, lots of business benefits – business reorientation I’m sure Phil especially is an expert at talking about – but we have a particular interest in new processes, new design systems and new materials. We’ve worked through the last ten years, through the Noughties if you like, on single-material Additive Manufacturing and our research focus now is on depositing multifunctional, or the creation of multifunctional devices: depositing different materials, mainly by jetting processes to produce multifunctional devices rather than just clever shapes in single materials.
PH: Yes. Finally, Mark.
MM: It has just occurred to me in this process that everyone, or I’ll assume everyone in this room, knows what 3D printing is and…
PH: We’re getting to that later.
MM: You’re getting to that later? OK, ‘cause there’s quite a lot of detail coming out! I come from a slightly different background from these guys because I’m a material scientist, interested in materials and the stuff that everything’s made of. For a long time I’ve been collecting materials, making a materials library – we have it at UCL. It’s an extraordinary thing; it’s sort of the DNA if you like of all, everything that’s in the V&A, you know all of the ceramics, the glasses, the metals, the enamels, all of that. You know, all the raw stuff that that stuff comes from, and material scientists around the world create new materials: materials that change colour, that do weird things under different electric and mechanical fields – there’s a ferrofluid black skull downstairs which is a good example of this if you haven’t seen it. So, the collection got more and more complicated and weird, and that was only great for us. And then someone placed, it must have been five or six years ago, in my hand a material and said “what’s this do you think?” And it was like your [PH’s] necklace but it was a bit less complicated, and it was [an] intricate chain mail object and it had no joins in it. He said “I had no idea, I mean I really had no idea that you could make something that intricate, with moving parts, with no joins” and it turned out that it had come from a 3D printer. That was my first entry, and I… so like I say I’ve been collecting materials for a long time and I’d seen a lot of weird stuff and I realised that this was a significant moment in the history of materials, and making stuff, and I just, you know, I couldn’t then not get involved, really. Now we have the Institute of Making, we have many, many 3D printers, and I guess my interaction with them is as a user. I mean, we try and really work out what materials you can make with it, and how you can change the properties of those, and why the materials’ properties are so different from the other ways of making stuff. That’s me!
PH: Wonderful! Yes, as you said we cannot at all assume that everyone in the room is as familiar as you guys might be with the ins-and-outs of 3D printing, so Adrian: would you mind quickly explaining? If I were to send you a digital model and you were to print it out on one of your lovely RepRaps, how exactly would that work? What would happen?
AB: Do you want me to say specifically how the RepRap works or how Additive Manufacturing in general tends to work, regardless of what process we’re talking about?
PH: Let’s go with sort of a general…
AB: The principle difference between 3D printing and conventional ways of making things… let’s start with the conventional ways of making things: conventionally we cut things out. Normally if you want to make a thing, what you do is you start with a solid block and you chop the bits away that you don’t want, and there are a whole variety of processes for doing this that we’ve had since the Industrial Revolution 300 years ago. Additive Manufacturing is the reverse: there you start with nothing and you add material to build the object up. Specifically, and most commonly, you add the material in layers. You start with a flat sheet and you put a single layer of the object, a very thin layer down, and then you put the next layer on top of that, and the next layer on top of that… and it’s a rather slow process, much slower for example than cutting things out. The immediate question arises: “why do we bother when cutting things out is much faster?” The answer is: because it turns out that by adding material as opposed to subtracting it you can end up with a far more versatile set of shapes in the final product. The reason for that is a mathematical one, which we can go into. I don’t know if you want me to do that now, but it is quite an important reason to do with a number of dimensions in which you have to solve the problem of how to make the thing. I won’t mention that now but if Pippa wants to come back to it?
PH: We’ll come back to it.
AB: Anyway, so we’re adding material in layers one at a time, one at a time, one at a time, and there are about half a dozen main different ways of doing this. Pippa asked me to mention how the RepRap does it, and the RepRap machine does it in a process that wasn’t invented by me or invented by anybody on the RepRap Project – it was invented about 25 years ago, and pioneered by a company called Stratasys. The way that technique works is essentially with a computer-controlled glue gun. If you can imagine taking an ordinary glue gun from B&Q: as you push the glue stick through it, it melts of course and comes out of the end in the form of liquid glue and you can use it to glue bits of wood together and so on. Now imagine you took that glue gun and you controlled its movement, moving it around with a computer. You could take a flat sheet and you could move the glue gun over the surface of the flat sheet, squirting bits of glue or not squirting bits of glue, to form a single layer of glue over the flat sheet. You could then move the glue gun up a little bit and form the next layer and then form the next layer, and form the next layer and so on until you ended up with a three-dimensional solid object. In the case of a glue gun it would be a rather crude object because the glue is very splodgy but if you miniaturise the nozzle, make it much, much smaller in diameter, and you change the glue to a conventional plastic, for example such as ABS which is the plastic that Lego bricks are made out of, you can actually make a rather fine object by this process and you end up with the sort of thing that you can see magnificently decorating this giant Christmas tree to my left. So, the process is one of adding things in layers. The particular process that I’ve mentioned, the computer-controlled glue gun, is one of about half a dozen ways of adding stuff up in layers.
PH: Wonderful! Right, so Richard: do you want to explain? If I had a bit more money, and [laughter] yes, what could I achieve in a slightly more… what are the other methods of producing a 3D printed object?
RH: There’s very much a split between the prototyping and low-end 3D printing kind of technologies and the technologies that are used for what we call Additive Manufacturing. The predominant manufacturing-based processes at the moment, and I’m not convinced that these are the ones going forward, I’m sure Phil agrees that they’re not the ones going forward, but the predominant ones are the powder-based technologies that you then fuse with a laser, so not the powder-based technologies that you bind together with a jetting kind of system, Zee Core kind of processes. The either polymer or metal-based powder systems that predominantly use a laser, but in the metal-based systems you can use an E-beam for example. So you would, in the same way that Adrian was explaining there… the thing that links all of these technologies: you get a CAD model or 3D data in some form, you chop that into a bunch of slices; you orientate it into the way you want to build it, you chop it into slices and then print them in one way or another. In the powder-based systems you just scrape a layer of powder, typically 0.1 mm thick, and you fuse it together with a laser and then that carries on. The advantage you get from the powder-based systems is you get much more design freedom, so all the very clever intricate designs are really produced on these selective laser-centring polymer systems, so this lovely necklace that Pippa is fashioning for us here. You don’t get the same design freedoms in the metal-based processes: you have to have support structures because of the thermal gradients that you have, but they are the predominant manufacturing. For the future: future systems are definitely going to be jetting-based.
PH: What does that mean?
RH: Ink jetting. So in a way we’re going from like laser 2D printers to ink jetting-based systems so I think if you want, or certainly in our area where you want to do multifunctional devices, you need to be able to selectively deposit the material where you want, and you can’t do that with these powder-based techniques. You have to be able to selectively deposit the material very precisely with jetting-based systems. The problem then becomes, I totally agree here, is that materials are the issue. Materials and design are the main issues with Additive.
PH: Right. Super. Now that we’re all up to speed, I think we should have a little… I want each of you, well I asked you last week to have a think about this, a think about what is amazing now, because obviously we’re going to go on to talk about the future but let’s get a few examples of what we’re doing now in 3D printing, or what’s special now in 3D printing. So, let’s… do you want to start?
MM: Oh great. Well, the thing I think is most… the great thing about this technology, apart from everything that’s been said already, is that of course you can make an object exactly tailored for someone. At UCL last year there was a patient who had throat cancer. There was really no hope for them: they were going to have their windpipe taken out and they were going to have to speak for the rest of their life through a kind of voice box, or they were going to have to grow a new windpipe. Now, there’s this technology now where you can take a, you can get a scaffold which is exactly the same shape as a person’s windpipe, because you can take a MRI scan, get your 3D CAD file, and then you could print that scaffold. Once you’ve got the scaffold, which is a biomaterial that essentially is eaten away by the stem cells you then deposit on it, if you take the stem cells from the patient – which is what they did; they put it in a little bioreactor for a few months. They grew, in the exact shape of this person’s windpipe, they grew another windpipe made from their own stem cells, and they’ve implanted it and that patient’s alive today, able to speak. It may all fall through. It may not vascularise, it may not do lots of things, but it’s going to have a massive impact in medicine with all sorts of hip implants. I mean, this is very very avant-garde stuff but it’s the state of the art, and so I think I very much doubt in the future that anyone in this room will not benefit from 3D printing or Additive Manufacturing of some of their body parts in the future. Sounds a big claim but I would stay by it!
RH: I don’t buy into this “you can make anything” on these systems thing at all. You can make probably any shape but you can’t make any functionality, certainly at the moment, and in the future that’s the debate – you probably can do. I think generally the most interesting thing about Additive at the moment is the design freedoms and this freeing up of geometry and we see it in lamps and dresses and shoes and all these kind of things, but I think one of the best examples of a product at the moment that is produced in millions now is the in-ear hearing aid. They are perfect for Additive because they’re small and complicated and therefore very cost-effective to make – they make it on one of the higher-end systems. Actually on a photolithography-basis, and a light-sensitive material based system and they are based on the person’s geometry. So I totally agree that the human-based parts actually are the most attractive thing for it at the moment, and so these in the ear hearing aids cost, you know, dollars to make, very few, very little amount of money and they give tremendous benefit to the individual because they’re customised, tailored and they’re great for the company because they’re cheaper to make actually than the conventional way of doing it. As an example today then it’s the hearing aids for me.
PH: Phil?
PR: Yeah I think for me at the moment the one thing that’s really opened our eyes is, obviously, business disruption is a big thing with this technology, and the idea of democratising manufacturing. We’ve talked about it for nearly a decade now. If anyone’s been following it, there was a fantastic project called Robohand which kind of sprung up by accident, which was a guy in South Africa who was a woodworker who’s pretty crap at woodwork because he chopped his fingers off, which isn’t really what you should do if you’re a woodworker! He was told it was going to cost him tens of thousands of dollars to get a replacement hand and that’s something he couldn’t afford, and there’s no healthcare system that provides, so he went searching the internet and found somebody who would design a product. They’d worked in the animation industry, and they designed him a hand which could be 3D printed. That’s great, that’s a nice start to the story, but what then happened was people saw that on the internet and started approaching him saying that they had children with something called Amniotic Band Syndrome, which is something that happens in the womb where you end up with a loss of digits. He realised quite quickly that he could modify his designs and make those designs for individual children and then it went viral because everyone realised that anyone could make these designs for anyone’s children. We did some research on this and there’s 90,000 children a year born with Amniotic Band Syndrome; there’s 100,000 consumer 3D printers in the world. We printed three out last week and it took us four hours. There’s no reason why we can’t, quite simply, print all the world’s demand for a product from a social position.Now, from a business position that then starts to become quite worrying if you’re a healthcare company, because actually do we need healthcare companies in the same context? Obviously there are certain mechanical issues and regulation and legislative issues, but for a simple product like that I think it’s shown us how disruptive this actually could be. I think that would be my kind of take on what’s quite interesting at the moment. Adrian?
AB: I’d like to say the things that I think are the most exciting and interesting aspects of 3D printing at the moment are the least exciting and interesting things being printed - that sounds very oxymoronic, let me explain what I mean. This is a cheap Casio watch. I’ve had it for ten years; it’s essentially worth nothing. Keeps perfect time, it’s not worth a thing. A few weeks ago this little strap that holds the main strap on to my wrist and stops it flapping about broke. I have no idea whether you can buy one of those or not, probably it would be rather difficult to obtain because the watch itself is so cheap that you’re not going to sell spare parts to it. But I didn’t even bother to look – I just printed out one on my RepRap machine that lives in my workshop. It’s now holding my watch together which now has another three or four years’ worth of life in it. It took ten minutes, which is less time than it would have taken me to drive to a shop anyway. It seems to me that you need really powerful technologies to do all sorts of useful things, like medical engineering which has been discussed and so on, but you need exceptionally powerful technologies to produce trivia. That’s the reason why 3D printing is exceptionally powerful.If we look at our current most important manufacturing technology it’s injection moulding - the way the strap of the watch was made and the way in which that little loop was originally made by Casio. Injection moulding, as I say, is humanity’s most important manufacturing technology and it’s the one we use to make things to put in Christmas crackers. Why do we use it to make things to put in Christmas crackers? Because it’s so powerful that it’s easy to make trivia with. 3D printing, it seems to me, is exactly like that: it’s such a powerful technology that people can use it to make a carrot holder. You didn’t know you needed a carrot holder. Somebody designed a carrot holder with very good intentions. What they wanted to do was to hold the carrot off the floor of the rabbit cage so it didn’t get dirty and the carrot could be eaten by a rabbit who then got a clean carrot. Now no industrial company in the world has perceived that there’s a market for carrot holders, and yet this person printed themselves a carrot holder. They were happy with their carrot holder. If they ever only printed one carrot holder then they’ve achieved what they wanted to do. A carrot holder is essentially a trivial object compared to the complexity of the internal combustion engine and a motor car, but the fact that this technology allows people, using a machine that costs the same as a laptop, to make all sorts of things like carrot holders and little loops on watch straps, that they just happen to want, seems to me to be to be the most exciting aspect of it all.
PH: Wonderful! I think it’s more than time to open questions up to the audience. So, does anyone have any questions for our panel? Hands up!
Q1: Yes the question I’d like to ask is: the technology, the electronic technology obviously is going to go from strength to strength, as digital photography did, but what about the physical attributes of whatever the nozzle or carver or whatever it is at the other end? How small can that go? Can it go into the microscopic detailing, because it seems to me that that is the thing which makes 3D printing fairly crude at the moment – it looks like Lego bricks under a magnifying glass.
PH: Yeah, Richard?
RH: The, well I mean you can go beyond the micro to the nano actually so you could use something called T-photon lithography [where] you can produce very very very small nano-scale parts. I’m not totally convinced that we will – I’ve got a centre working on multifunctional Additive Manufacturing, looking at combining printing electronics and structural parts, so printing the system in one go. So, you’d think I’d buy into this concept of printing the lot. In reality, as with current printed electronics, you’re not really going to print the electronics - you’re going to print the connections, and I think silicon is so cheap and so small you can pretty much just chuck it in, so long as you can make the connections. It’s probably the way to go I think, or certainly any time soon. Could you print the transistors? Could you print all these things? Well yes you could but it’s not going to be as good as silicon. But can you get the level of resolution that you’re talking about? Yes, but for very small bits, and then for making bulk parts from that it’s very difficult. The difficulty comes in trying to make a reasonably large part like a phone and the microelectronics and nanoelectronics at the same time. Having a system that could do all of that is a complicated thing.
PH: Very good question.
Q2: It seems fantastic that you can sort of make multi-material parts, and also print off carrot holders and things whenever you want. Is there any prospect in the future of their being able to then take them apart so they can be more easily recycled using 3D printing, sort of just suck it back up, or is that still science fiction?
PH: Yes, Adrian?
AB: It depends of course on the materials you’re using. As Richard indicated a little while ago, the current generation of machines that are out there in production now tend to work with a single material. That’s a great virtue from the perspective of recycling: you’re in the position of only having one molecule to deal with. As soon as we get to the thing that Richard said more recently, namely multifunctional parts with electronics embedded in them and so on, the recycling problem of course gets much more difficult because you’ve got somehow to separate out all the various components. On the other hand, there are some aspects of 3D printing which particularly lend themselves to recycling. One of the most commonly used materials in the very low-end cheap machines, the type that I’m concerned with, is a material called polylactic acid, which is a biologically-based polymer: it comes from starch. That’s completely biodegradable and recyclable, and in fact it’s actually quite easy to make – we’ve made it in our workshop ourselves from starch. So, you’ve got a rather interesting recycling route here in that if you’ve got enough tens of square metres to grow a starch crop, you can make your own supply of material for your 3D printer, and when you get bored or fed up or break the things that you’ve made you can chuck them on your compost heap and they go back into your potato crop for the next starch for the next 3D print. You’ve got a local recycling loop, not involving trucks running up and down motorways at all. The compost heap has to be a proper high temperature one, but apart from that there’s no problem in principle with what I’ve just described. Dealing with single materials: great. With multiple materials, as with all recycling, you’ve got the separation problem and this technology probably makes that even more difficult than it does for an assembled product because the bits that need to be separated are actually physically embedded in other materials.
MM: I just wanted to add something about that. That’s currently how it works at the moment, if you wanted to do recyclable. But actually look at the body: the body uses very few raw ingredients and creates things that are stiff or plastic; it creates things that have optical qualities and it has electrical connections in it, so what’s really amazing is that it’s going to be possible. It’s going to be possible to do exactly what you said and have multi materials, but made from a basic set of ingredients, and still have electronics and optical things and do the multi materials. That’s the material science bit that has to be done, and is a very exciting area to be in.
PH: Great, wonderful question. Have we got a question over here?
Q3: From the perspective of the future of digital printing and the latest changes in the curriculum that are about to possibly go through, in relation to design and technology, which involve children from the age of five understanding programming and how to 3D print: what impact do you think that will have when anyone from the age of, say, five in the future can 3D print anything they want? What impact do you think that will have on the future and industry?[Discussion amongst the panel]
MM: Right I’ll have a go, I’ll have a quick go at that! I mean I think this is… In our Institute we have lots of 3D printers but we also have all the basic tools: we have the chisels and the screwdrivers and we have all the drilling and the bandsaw, and we have exotic things too like laser cutters. And what the 3D printer… it’s clear what’s happening: 3D printing is a way in to making stuff for people. They come and they 3D print and then they realise that the limitations – that actually they can’t do what they wanted to do in every case, in most cases in fact – then we say “well actually you can do that on the lathe or you can do that on a milling machine, or you can just do that with a…” and it sucks them in to making as a culture, as a thing, as a way of relating to the world. So, I only see the positive here. I see it as a way in. It’s like books in a way: books bring you into the world of intellectual thought and I think 3D printing will bring you into making.
PR: I absolutely agree but I think the key issue is that you can’t get away from problem solving and there is an element of using 3D printing to cover up good problem solving, i.e. I had a rabbit when I was small and I didn’t want to get rabbit poo on my carrots so I just stuffed it into the side of the rabbit cage. Hey presto: one clean carrot!
AB: Half a clean carrot - it couldn’t get to the other half!
PR: I’d already pre-cut it for the rabbit; he was really happy! I think that’s one of the things that comes back to Richard’s point that yes you cannot do everything with these technologies. You have to understand the limitations of what can you do and what can’t you do, what is the appropriate process for the problem you are trying to solve? I think if that’s embedded in the curriculum that’s great, however my biggest fear is that we just generate – create a whole generation of rampant consumers who, whether it’s PLA or ABS or recycled HDPE, make things for the sake of making things in some belief system that actually it’s ecologically friendly because it’s not being made in China. I think you could so quite a lot in the whole education process to use 3D printing as a catalyst to understand how supply chains work, how consumerism works. I think it’s probably broader than just squeezing plastic from a nozzle.
PH: Can I just point out: all the acronyms you just said in the middle there, those are all types of plastic weren’t they?
PR: Well polylactic acid, high-density polyethylene…
PH: We’ll believe you!
RH: I think one of the problems we have at the moment in our consumer-based society [is] actually most people don’t care how things are made, alright? So I think making a connection for people about how things are made is really really important. There have been quite a lot a schemes about putting the low-end 3D printers into schools, which I think is a great idea. But that tends to be high schools and I think they’re lost by that stage. We’re doing something at the moment of putting them in to junior schools and primary schools so you can get them at seven, eight, nine, when they’re still excited by these kinds of things. I think that’s important. I totally agree with Phil that there is a danger of just creating a bunch of landfill, a printing landfill of these things.
Q3 responds: I have a young son who, you know… again it’s the balance between the consumer society of every time there’s an advert on TV – “I want that, I want that!” – and if children have that capability of making what they want, like you said, when they want it then it’s balanced with the other side of this Maker Fair, which had 3D printers, the opportunity to see how they worked combined with traditional ways of making. I think I agree: the right education sort of translated in the proper way could be a route into understanding making and making perhaps a more sustainable world from that angle.
RH: The advantage of these systems are cool – they just look great! They kind of create things out of nothing. I’ve been looking at them for 20 years and I still love seeing a stereolithography machine, they still look cool. They are a way in to getting people excited by making, and understanding that you have to create to add value, I think.
AB: You mentioned five-year-olds having access to this technology. A brief anecdote: Neil Gershenfeld who’s the Professor who runs the Center for Bits and Atoms at MIT – he’s the person who created the Fab Lab which is basically a container-sized manufacturing laboratory which can be dropped virtually anywhere in the world. One of the things they’ve done with those is to take them to sub-Saharan villages in Africa and get people in making micro controllers, building small mechanical devices using the technology, development and so on. One of the things he discovered was that you can get an eight-year-old in there and she’ll be making a micro controller in a day; you get a 35-year-old in there and they just can’t manage it because their brain’s, as is my brain, completely ossified by that age. The younger you get people, the better. There is, well there must be a lower age limit, I doubt whether people 18 months old can handle the technology, but certainly eight, nine and ten-year-olds have no problem with the concepts whatsoever and that’s the time to get it. Incidentally, rude things have been said about landfill. I’d just to speak up for landfill. Small point: I mentioned that polylactic acid is plant-sourced. If we can figure out a way to stop it from biodegrading, which shouldn’t be too difficult, what we should be doing is encouraging people to make junk and then throw it away because it’s plant sourced, so all the carbon in it came out of the air. If you make a lot of polylactic acid junk and put it in landfill and it stays in landfill you’ve locked up a lot of atmospheric carbon. So it may well be that a throwaway culture is the one way to save the planet. [Laughter]
PH: Right! On that note we should probably move on to…
RH: We’re not going to let him get away with that, I’m sorry! No no no.
PH: I think we should probably… with 35 minutes in and we haven’t actually talked about the future yet, which is the title of this session! So, I would like to know where we’re going to be; how is 3D printing going to affect me and this audience in the next five to ten years, and then in 50 years’ time? Over lunch we did talk about how ridiculously speculative talking about things in 50 years’ time is, but none of you are going to remember so it doesn’t matter what you say! Just make it entertaining!
AB: Right OK yes as Pippa said none of us know what the future holds. Indeed studies have been done on this by serious psychologists: they will tell you that experts don’t know any better than anybody else what’s going to happen in the future. One exception being experts who actually predict for a living and get feedback on their expertise; weather forecasters for example know what the weather’s going to be like tomorrow because they’ve had a lot of tomorrows to study the results of their predictions. Ask a banker what the bank rate’s going to be in a year’s time and they won’t have a clue! We don’t know what the future holds. I think in five to ten years’ time what we’ll start to see with the low-end machines, which is my area of speciality, is what actually happened with two-dimensional computer printing. I don’t know if you remember this, it’s so long ago, ooh eight years, that we’ve all forgotten. It used to be that there were little print bureaus on the corner of every street where you could go and you could have, for example, party invitations printed because the laser printing technology, the laser printing machines cost, you know, a couple of thousand pounds. So the technology moved from industry to what was then the high street – of course what that now would be is online bureau services – and then ultimately it ended up with most of us owning our own little Hewlett Packard inkjet printer, which we only use once or twice a week. One of the interesting things about technology when it gets cheap enough is that we don’t care when it sits idle. You’ll have a robot in your kitchen that does your laundry; you paid two or three hundred quid for it; it sits idle 90% of the time and you don’t mind. If you’ve got a 3D printer in your spare room, that just sits on a tabletop, and it sits idle 90% of the time, and it costs the same as the washing machine, you won’t mind that either. Just occasionally it will come in useful to make something trivial – a coat hook, you know, you need a coat hook to stick on the back of a door. An economist once told me that the world market for coat hooks is bigger than the world market for jet engines.
PH: That’s a wonderful statement!
PR: Coming from a company called Econolyst I would not trust economists! I’d go with the jet engine!
AB: That’s why I prefaced my remark with “an economist once told me…”[Laughter]
PR: I think Adrian’s got a really good point that if you look at the history of 2D printing that yes, we went from the printing press, we went to digital – digital was great big factories - and then it ended up in the home. What’s interesting is most people – I haven’t had a printer in my house for about ten years; I have one in my office but not in my house. Anything like photographs we now get printed by online fulfilment. We don’t know where they are; all we know is that they arrive 24 hours later, perfect customer service and we should go tell somebody else.
AB: Not at all! I print at home!
PR: But do you? I shall share with you: it took over a week to [3D] print all those little heads! [Decorations on the Christmas tree] The machine failed, probably two times out of three to print those. The technology is not robust in terms of the process – [the] technology’s not robust to make continuous products. The material properties are inferior, the economics actually don’t stack up – it’s cheaper to buy a Super Mario made in China off the internet than it is to print a Super Mario on your Replicator 2X using $30 filament. We’ve got a long way to go before this actually becomes economically viable, technically credible and socially useful. However, within the industrial domain I think we’re going to see some profound changes in the next ten years in the same way that we did within commercial printing. We’ll see this finding its way into more and more and more vertical markets, whether that’s aerospace or automotive or medical, which is already the biggest market for this and as Richard said it’s all about making personalised, customised, individualised products. It’s perfect for that. We only scratch the surface at the moment, so I think we’ll see more products, but as Richard also pointed out nobody actually cares how products are made; you don’t often question how they’re made.
RH: Following on from that point, I think that we won’t see every house having a 3D printer. I think that people, even if you can excite them through 3D printing, I don’t think every house will have one because I agree with Phil on the “you have your photos printed at a hub or a booth or you get them sent online.” I think that’s what we’ll do. One of the problems with Additive is that not everybody can design either, alright, so you’ve got to get the content from somewhere. You’ve got to be able to use a CAD system, and they are getting easier but they are still relatively complicated to do. Not everybody can design. You might be able to download the things but will your system at home have the complexity? Certainly in the next five ten years I don’t think so, to be able to produce anything more than trinkets and Phil’s face on a Christmas tree. I think to get the level of fidelity out of a component and the structural integrity for things that you actually genuinely need, bits for your motorbike or your car or what have you, then you can’t make those, really, on the low-end printers that you find in the home. You’re going to have to make those on higher-end systems, which will have to be more hub-based. I think we will see a proliferation of devices – the reason these low-end systems have proliferated is because patents have expired. We’re beginning to see the patents expire on the higher-end systems, the powder-based systems and the jetting-based systems, and so you will see a whole new bunch of technologies coming to the market but they are going to be more professional systems than home-based systems. You’ll definitely see more companies using these: we are already seeing a marked increase in companies using these technologies. But, in the home – I personally don’t buy it.
PH: I was going to… quickly, your point in that: I might not have a 3D printer at home in ten years’ time, but…
RH: You will use it, yeah. It will touch your life, yeah, for sure.
PH: But, so I’ll have… there’ll be lots of items in my house, so you think?
RH: There are lots of things that you can buy now that are 3D printed: lamps, hearing aids and bits for cars.
PH: Expensive jewellery…
RH: But they are beginning to creep in. There’s lots of… in the dying days of Rover, because they couldn’t afford the tooling they used to 3D print parts for some of their lower-end cars because that was a way of getting the product to market, so they could sell things. There’s quite a lot of Rovers out there actually, and the later Rovers rolling around with laser sintered parts on them.
PR: I was going to say, with 40,000 hip implants put in last year that were all made Additively, I don’t think a single patient actually knows they have an Additive hip implant and I’m sure they don’t actually care. What they know is that they don’t have a horrible pain in their side. Similarly Dentor – there are a couple of million dental crowns that were laser melted. We don’t question it; it’s another manufacturing technology in a toolbox of technologies.
RH: Yes, I agree.
PH: So there could be someone in the audience with a 3D printed tooth that they don’t know about?
PR: It’s highly likely!
RH: Very likely.
PH: There we are! Cool, sorry, yes? Ten years in the future?
MM: OK ten years in the future. There are lots of things. I agree with much of what’s been said. I’ll just pick a top… I mean I think there’s lots of other areas but I’ll pick one. I think repair will become a very different thing, I think already at the moment. It used to be that if you went to repair your bike or your washing machine you had to look at the manual, and there were these terrible diagrams. If you get the Haynes Manual it’s better, but even so, difficult. You got discouraged quite easily and then you had to find the parts, go round the thing and they weren’t there… anyway, so it was a palaver. In the end, these days, the people who repair stuff they really just haven’t got enough friends, mostly. It’s just easier to buy a new washing machine than to repair it, once you encounter it. Now this is madness. There are three parts that fail in a washing machine, otherwise the thing would last for 20 or 30 years. If those three parts could be printed out you don’t have to have huge logistics on warehousing them all, or my boiler for instance: I had to get rid of my boiler, not because it didn’t work or wasn’t repairable but because the part didn’t exist any more. Imagine a world in which, actually when you buy something, all the digital information is given to you too.
RH: Would you then print half your boiler at home then?
MM: No I don’t think you’d print it, you’d get the best, but essentially you are in control of your technology at home. If it breaks not only have you got these parts that you can print but actually these days, and I’m sure you’ve all done it, you just Google “fix hinge on Zanussi type 3…” and there’ll be a video. Someone’s done it, a little hand-held video and “I did this, and I did that” and it’s so useful. You can re-record it, you can stop. I’ve repaired so many things because those videos exist. Now, put the videos with the 3D parts and I think you’ll have a repair culture, and a longevity of technology which I think would be really enriching and wonderful, and we could really do it. I don’t think there’s anything stopping us doing it, and that’s a nice thought.
PH: Or we could pay somebody to do it for us as well? I suppose.
MM: Yeah we could pay somebody to do it, but it should…
PH: We’re not going to get rid of mechanics! That’s my point.
MM: Um, no I’m not saying that. I’m saying that I probably would have someone, a CORGI registered someone, doing it for my boiler!
PH: Yes, that’s what I mean!
MM: I would like to make that clear![Laughter]
PR: Just to put some metrics to it: we recently did a study for a washing machine company. If you try to 3D print the printable components of a washing machine today what is currently a $300 bill of materials goes up to $12,500, OK? It comes down to $500 in five years’ time and down to $200 in ten, and that’s if you use the trajectory of current 3D printing technology moving forward. So, maybe it’s not that unrealistic in a ten-year period to suggest that economically it’s viable. Technologically – we’ll leave it to these clever guys in their lab to work out.
PH: OK we’ve done ten years, now 50 years. So you can get silly now.
MM: Is there anywhere to go, Adrian, after this? Can it get sillier?
AB: It’s very hard for me to get sillier than I already am! [Laughter]
PH: That’s very unfair!
AB: I’m bumping up against a brick wall here! The ultimate limit of silliness… hands up everybody who’s ever used a lathe? Oh good that’s a lot. Sorry, including myself.
PH: Christ that’s a lot! What a talented audience we have!
PR: Where did you use one?AB: OK. Well in my case Axminster but that’s beside the point. Yes, a large number of you. Now, in that case you would accept, I hope, that you’re probably not a statistically random sample of the normal population because most people probably haven’t used a lathe. I suspect in 50 years’ time 3D printing won’t be very important at all. Not because it’s not important now, not because it’s not important for the next 30 years, but there’s a technology coming up on the side which nobody’s even really thought about in this context at all. I mentioned earlier that moulding, injection moulding particularly, is the most important manufacturing technology that we use. Of course it’s trivial and completely unimportant compared to the most important manufacturing technology on the planet which is things growing - what you and I did, and oak trees do, and jellyfish do and so on. Increasingly of course biologists are getting a handle on that and in 50 years’ time we’ll be growing, I’m pretty sure, most of the things that we currently manufacture. That’s so much more a powerful technology than 3D printing possibly can be that we’ll be regarding 3D printing, though we’re all lathe users, rather now as we might regard the lathe in the context of this discussion.
PH: Wonderful! 50 years?
PR: I feel so much better now because I own 12% of the company that’s growing furniture, which my wife thought was really silly…. But I’m going to say Adrian thinks it’s a good idea! 50 years’ time: I agree we will live in a totally biologically driven world where we get biology to fundamentally do the things that we do mechanically now. Hopefully we’ll have done something a little bit cleverer to harvest energy; I think one of the best projects I’ve seen in the last few years was Marcus Kayser’s solar sintering, of using the sun. It’s capturing the sun and using it as an energy source for sintering sand together: 3D printing in sand in the desert using sunlight as your energy source. What a great start! OK it was pretty ropey, but that’s a really really nice start and I think, with a little bit of engineering…
RH: He made a bowl.
PR: He made a bowl, exactly, out of sand heating it in a world where actually there are no ceramic Additive Manufacturing vendors, really, that make ceramic of that quality. Biological energy sources and materials have got to be the way forward but I don’t know, I’ll be long gone by then - you should see my diet![Laughter]
RH: I am going to disagree with Adrian here, I think, that I just don’t think that everything is going to be biologically manufactured. To think “oh you’re just going to biologically grow your car” - I just don’t think so. I think it’s going to have to be manufactured.
AB: You can do, it’s called a horse, but yes.
RH: No I think… but that’s a horse and not a car with four wheels!
PH: A genetic modification?
RH: I think that we’ll certainly have, I mean if I look back 20 years ago, at what we were doing 20 years ago, you’re beginning to see those things now in the general public. I’m hoping that in 20 years’ time the multifunctional stuff that we’re doing now will be out there and commonplace and everybody will be talking about it. So, I can buy into printing systems, and that’s what our research is about. I think there will be much more biologically inspired stuff. I mean we’re beginning to see biologically inspired design through things like topology optimisation, and all these lattice structures. The key aspect you get with Additive is the ability to make complex geometry and then add complexity to that through functionalisation and what have you. I think that that ability to deposit material where you want it, it could be biologically driven material that will enable you to produce the parts, but I don’t think we’ll be growing everything. I think 3D printing is the logical way of making things in many respects, and now all we need to do is create the delivery platforms to help us create the clever materials, and the clever designs that we need. The delivery platforms don’t exist at the moment.
MM: Yeah. I’ll get silly then if you don’t.
PH: Go on, someone has to.
MM: We will have a Moon base in 50 years’ time. Easy. Panel: Easy?!
MM: Well not easy, it’s quite tricky. OK sorry! Yeah yeah yeah that’s true. Damn.[Laughter]
AB: Will it be international?
MM: No no the Chinese, OK you’ve pressed me on that! The Chinese will have a Moon base. There’ll be a Moon base, hopefully it’ll be international. 3D printing is really well suited for exploring the Solar System and I think it is going to help us do that which is a nice thought really. You go to other planets, Mars, the Moon other moons around other planets – we’re going to need to make stuff. We’re going to need to live there for long periods of time, maintain the facilities, and we’re going to basically have 3D printers that are going to be able to take whatever local materials are there and turn them into stuff. I think we’re going to boot strap ourselves out into the Solar System with this technology. It sounds mad but I think that you’re going to need a sort of multi-functional maker something on any spacecraft going anywhere, because things will always break and you’ll need to replace them. To have any self-sustainable system off the planet we’re going to need these. I think they are going to help us get into space, which I am really excited about. It’ll do many other things too that these people have mentioned.
PH: Wonderful.
AB: Can I just briefly add a tiny sentence to that? People have flown 3D printers on the ‘vomit comet’ to see if they can work in zero G, which it turns out they can. We couldn’t afford to do that with the RepRap machine but what we did do is we ran it upside down. We know the machine will work in +1 G; we know it’ll work in -1 G; we conject that it’ll work halfway in-between in zero G as well.
MM: Extrapolation is so dangerous!
PH: Right we have seven minutes. Can we have some very short questions and very short answers, please? Hands up.
Q4: Do you think there will be a significant impact on supply chain, warehousing, obviously storing of materials, for manufacturing?
PR: You want a quick answer? Yes.[Laughter]
PR: No absolutely. If you look at the compelling business drive as why you use the technology then, as we’ve said, the idea of not having stock holding, not having redundancy of product – there are a lot of supply chains that EU legislation dictates you have to have stockholding of product. Cars are a good example: car manufacturers, even when they stop making a car, have to ensure that they can keep that car on the road for another 15 years, which means having mass stock holding or keeping old tooling and having redundancy in the supply chain. There’s lots and lots of issues there where [this] absolutely will change the supply chain model. I think then also how you change the retail model, because this idea of hub-based manufacturing, getting products close to the point of consumption – that will really cross a whole range of different areas, from healthcare through to just retail as it stands today.
Q4 responds: [Hard to hear] So there will be other impacts?
PR: Yes there will be a social impact and an environmental impact, but don’t get me wrong: this isn’t a panacea for clean, green manufacturing. Most of the current technologies are a heinous crime to energy consumption. We’ve got an awful lot to do to make these things sustainable technologies.
PH: Great, next question?
Q5: I have a question which is rather selfish: speaking as somebody who’s not even started their Product Design degree yet, and considering that this year graduates were making rapid prototyping machines at the New Designers Show, should I be feeling threatened that come five or six years’ time there won’t be a job for me anymore because of design democratisation?
RH: Absolutely not, I mean the design… so if you’re interested in Product Design and designing things then these technologies are manna from heaven for you, because you’re going to be able to, if you’re a very creative designer, be able to make very creative products. For years and years and years we’ve been teaching people to design for manufacture, to design for injection moulding, design for casting, and you’re limited in what you can do. Now we’re saying “actually pretty much you can make any shape you want,” not any thing you want but any shape you want. For designers it’ll be a brilliant time because most people can’t design. If you have an interest in design, you can sell your designs much much easier because there’ll be systems available to you. I think it’s going to be a great time for designers going forward.
PH: Good. That probably pleases a large portion of the audience. Hands up who…
Q6: I’d like to ask you, of the technology and from the perspective of small businesses: do you think there is actually a place for small businesses, like single-handedly led firms to offer manufacturing of small pieces like jewellery or replacement parts for your car knobs or whatever? In these times I’m quite interested in the development of new middle-range, middle-priced machines like Formlabs’ Form 1, which is about 3300 bucks and it’s quite precise, because what comes out of these lower-priced machines is quite crude and requires post-grading to use. Do you think that there will be suitable machines, and affordable machines, for small businesses?
AB: Yes is the answer, because as everybody said the technology… you’re absolutely right: the low-end machines, the machines that cost three, four, five hundred quid probably won’t give you the quality you want if you buy one today. One of the things we didn’t, or perhaps we did, I can’t remember, but in five years’ time – the quality in those machines is probably going to be just as good. Remember the Apple 2E? Little desktop computer? Compare that with a modern Mac. That’s the sort of improvement we can expect to see in five, ten years’ time.
RH: Why haven’t these…? These systems have been around for 20 years. Why haven’t the improvements… 20 years?
AB: 3D printing systems?
RH: Yes.
AB: Oh well patents. The reason is complete stifled development.
RH: So they just haven’t improved in this, particularly in that time?
AB: Yes it’s famously the case that after James Watt patented the patents he took out on the steam engine the entire development of steam engines was essentially stalled for 20 years until those patents ran out.
PH: OK time for one last question, and whoever it is has to promise to be really quick.
Q7: I’m wondering how modern copyright laws are going to learn to deal with a world where I can buy one thing off the internet and then post it to the internet for everyone to get for free.
PR: I can tell you exactly how that’s going to get solved because we’ve got the software code to do it! You’ll stream the data. The reason why the music industry and the film industry got into so much hot water over copyright infringement and data protection was that actually we weren’t all connected to the internet with 100 megabit fibre. Had we been, they would’ve just offered us streaming and we wouldn’t have had a proliferation of copied data. This idea that we’ll all be taking STL files and printing them out is a bit of an outdated notion. If I’m Pixar or Disney or whoever, I’ll just make the data you want available to you in real time, streamed and encrypted to your machine. Then you’ll get the product you paid for. Game over. You paid for a product; that’s what you wanted. So it’s the Spotify, Netflix type model of serviceisation, that’s what I think will happen.
AB: What about… I mean that was a scan of your head. [The Christmas tree decoration]
PR: It certainly was!
AB: What happens if scanner technology gets good enough that people don’t have to download what they want to print at all?
PR: Yeah but they’d have to have it in the first place which is this whole dichotomy of you have to have it…
AB: You can maintain things for your friends; that’s an infringement of the copyright.
PR: Well assuming my friends want a copy of my head, which I don’t believe they do!
PH: Are we talking about… so if I had a Nike trainer, say, or any other trainer technology, and we’re not at the level yet where you can scan it’s internal structure presumably, but if we get there and then is that going to be a problem?
RH: The thing that Nike do is a lot of materials research. You’re not going to be able to produce these things on your… I mean you can scan it, you can make the shape but you’re not going to have the lovely materials that they’ve spent millions of pounds developing. So I don’t think there’s an issue.
AB: Perhaps, going back to what Mark was saying a little bit earlier…
PH: Very quick…
AB: … about making materials with more different mechanical properties out of fewer base materials: you might not be able to use the same silicons and so on that Nike use, but what you might be able to do is create the internal microstructure in the material with your 3D printer that gives you the mechanical properties that Nike went for, even though you’re only printing with some rather rubbish plastic. You can put the microstructure in that Nike are getting the same effect of by doing all that materials research. I don’t know!
PH: That sounds like a 50 years’ time sort of job to me. Right we have completely run out of time, look at the clock! So thank you all very much for coming; I hope you enjoyed yourself and a big thank you to Adrian, Phil, Richard and Mark. To the V&A for hosting us, and you for being a wonderful audience and asking such wonderful questions.
Become a V&A Member
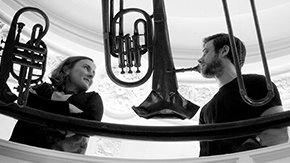
V&A Members enjoy a wealth of benefits, including free entry to exhibitions, previews, exciting events and the V&A Members’ Room. In addition, you will be supporting the vital work of the V&A.
Buy or Renew Membership Online